Making THE FLYING TIDINGS WHIRLED, 2018
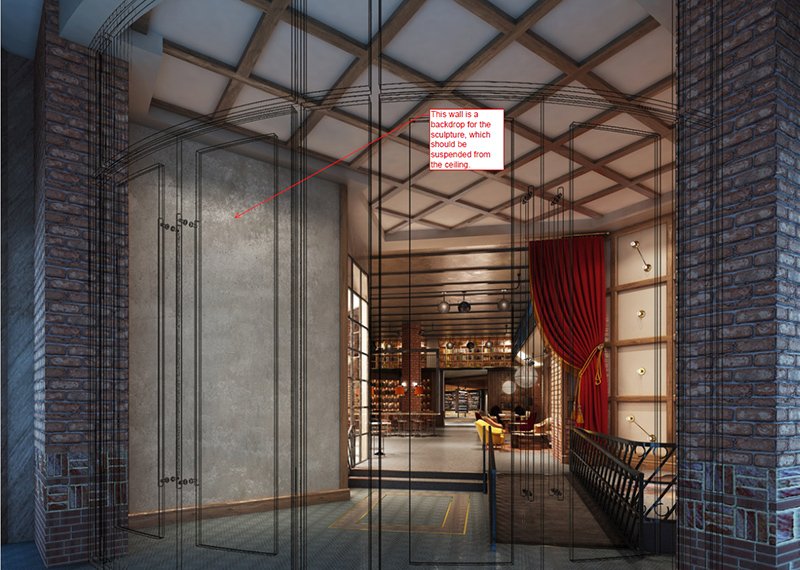
How do you come up with a concept for a space that hasn't been built yet? Good question! In the beginning of a public art competition, the client provides renderings and/or architectural plans of the site. Sometimes what you get is very minimal and you have to imagine what the space will be like. It's crucial to have a good imagination, an intuitive sense of 3D space...and to build an accurate scale model!
Some artists do everything on the computer, but I like to kick it old school with an actual scale model. A big reason for this is that I start my ideas for permanent metal sculptures exactly the way I do my paper installations: by cutting and sculpting cut paper. That said, with models the first pass is usually pretty rough. I'm not going for detail, I'm going for form, mass and volume...
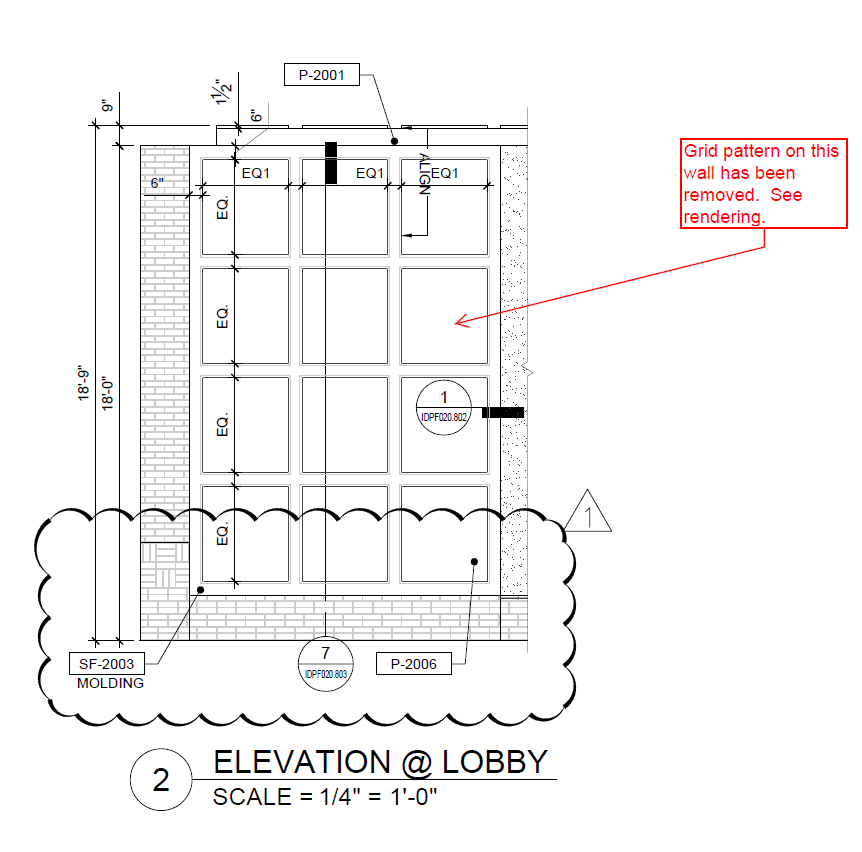
...I'm thinking about what will work in the space, how people will encounter the artwork, what it will look like from different angles, what kind of lighting it will need, what is safe and meets ADA requirements, and what I can do within the budget.

Because I wanted to represent all of the finishes that would be in the eventual built space, I decided to create my own seamless wallpaper of the textures: brick wall, penny hex tile floor, and concrete. This way I could scale and print them out to make a very realistic scale model. I was also excited to use my self-taught wallpaper design skills! Yes, I'm a nerd.
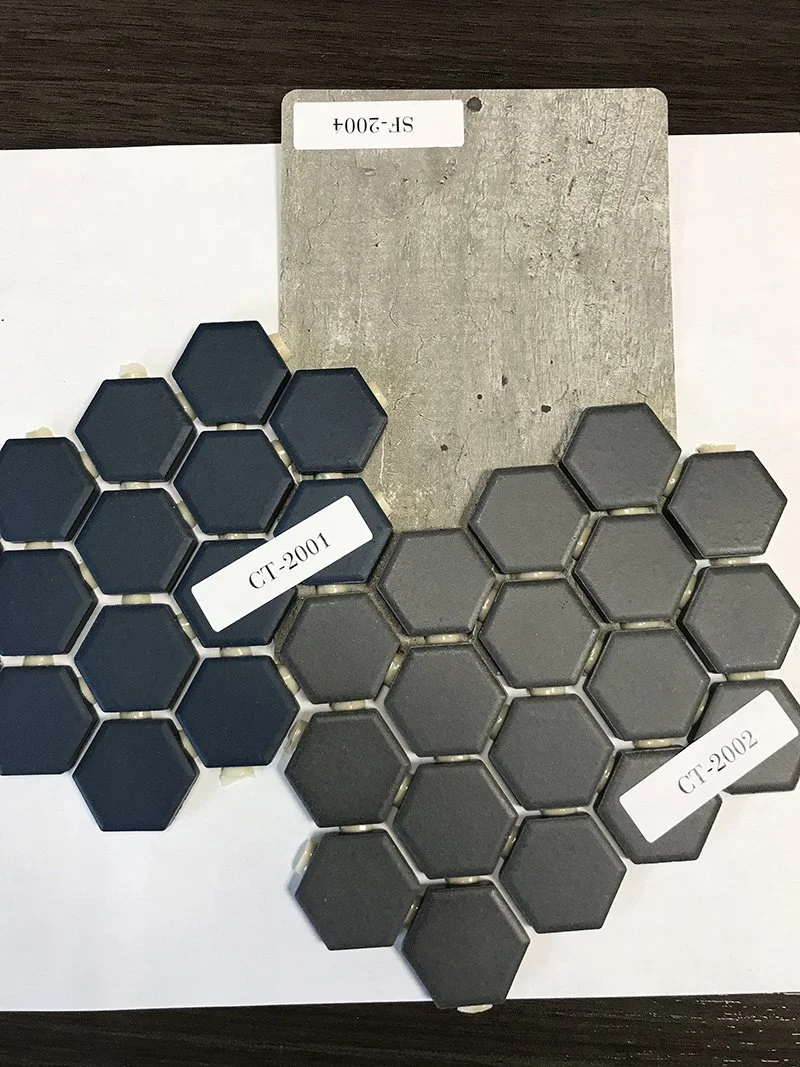
Photo from the client of their tile selection - that's how detail obsessed I can be. But I know from experience that the more realistic and believable the model, the better shot at getting the gig.
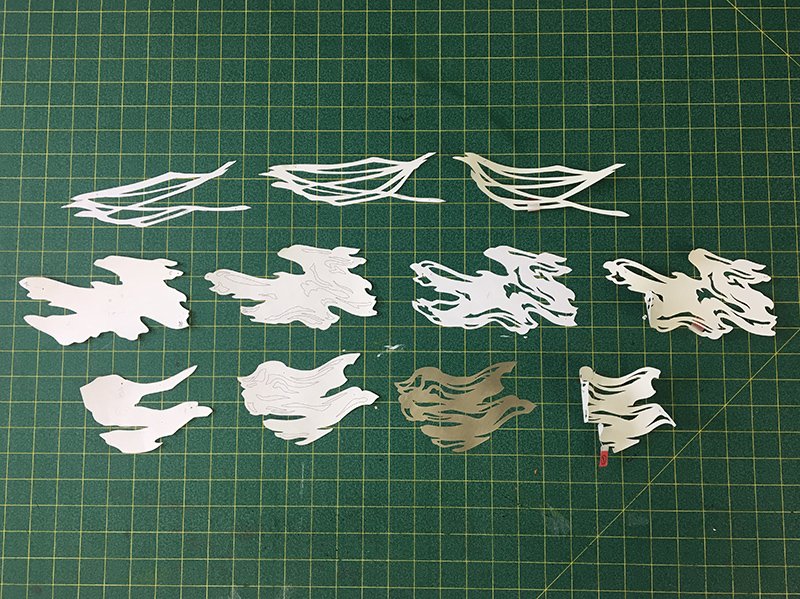
Here you can see how I iterate the pieces from totally rough (at left) to finished metal model parts (at right). In between, you can see how the final paper cutout (not shown) had been scanned in, traced and printed, and finally sent to my photochemical etcher to cut out of the scale material (nickel silver). After I finish and formed the model parts, I spray painted them white.
Here's the fancy new model on the floor of my studio with actual lighting! Spray-painted keychain flashlights make great model-sized track lights.
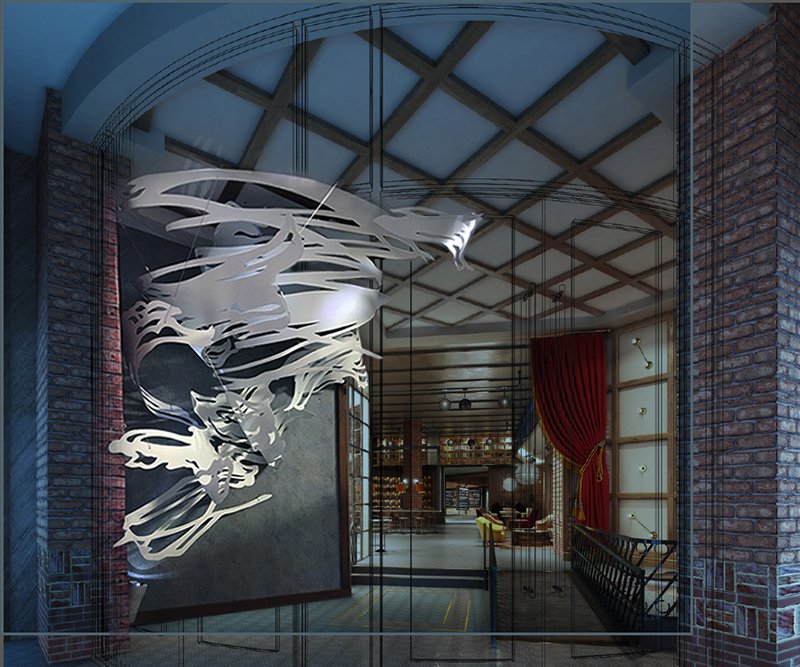
New rendering! Photo of the physical model Photoshopped into the client's rendering.
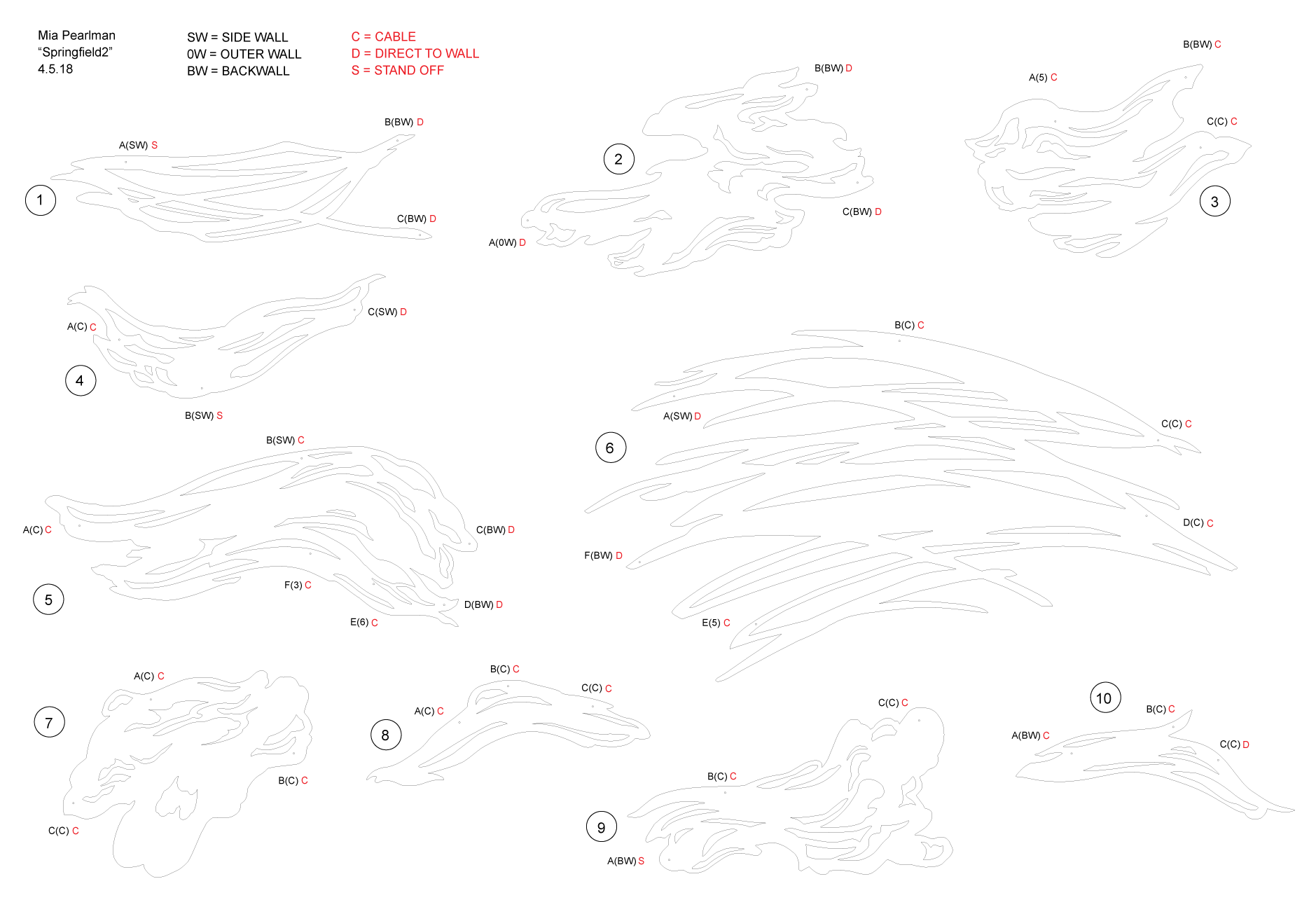
Yay, I got the job! Now what? We redo the model AGAIN to get all of the measurements and attachment locations exactly right. You don't want to find out the place you want to drill is already occupied by a beam, an air conditioning vent, or recessed light. This sculpture was particularly complicated, with multiple attachment types to the walls and ceiling, and about 30 kinds of hardware. Never know for sure what's behind those walls until you start drilling...
Now the real fun begins up at Polich Tallix near Newburgh, NY, among the best fine art fabricators in the world, but even more importantly, incredibly fine people. Mike List, their Manufacturing Manager, somehow finds time to almost singlehandedly make my sculptures while managing 30 people and several other projects. I'm so lucky to work with him!
Orbital polishing off the original finish from the aluminum manufacturer for eventual powder coating.
Watch Mike go! Here he is rolling the aluminum pieces so they exactly match the curves in my model.
The first couple pieces are up in the life sized mockup of the MGM Springfield space at Polich Tallix!
Pieces go up one by one...
And suddenly, it starts coming together. Always a thrill to see a sculpture transform from an idea to a model to a reality.
It's installation day! I'm not going to lie...this was a Murphy's Law extravaganza and literally everything that could go wrong almost did over the next few days. But these incredible professionals worked nonstop to install this sculpture, with a lot of patience and support from the RAREculture and MGM teams. I am forever grateful.
Sculpture or whale ribcage? You decide!
After much measuring, lifting, unwrapping and preparation, the first pieces go up in a very specific order.
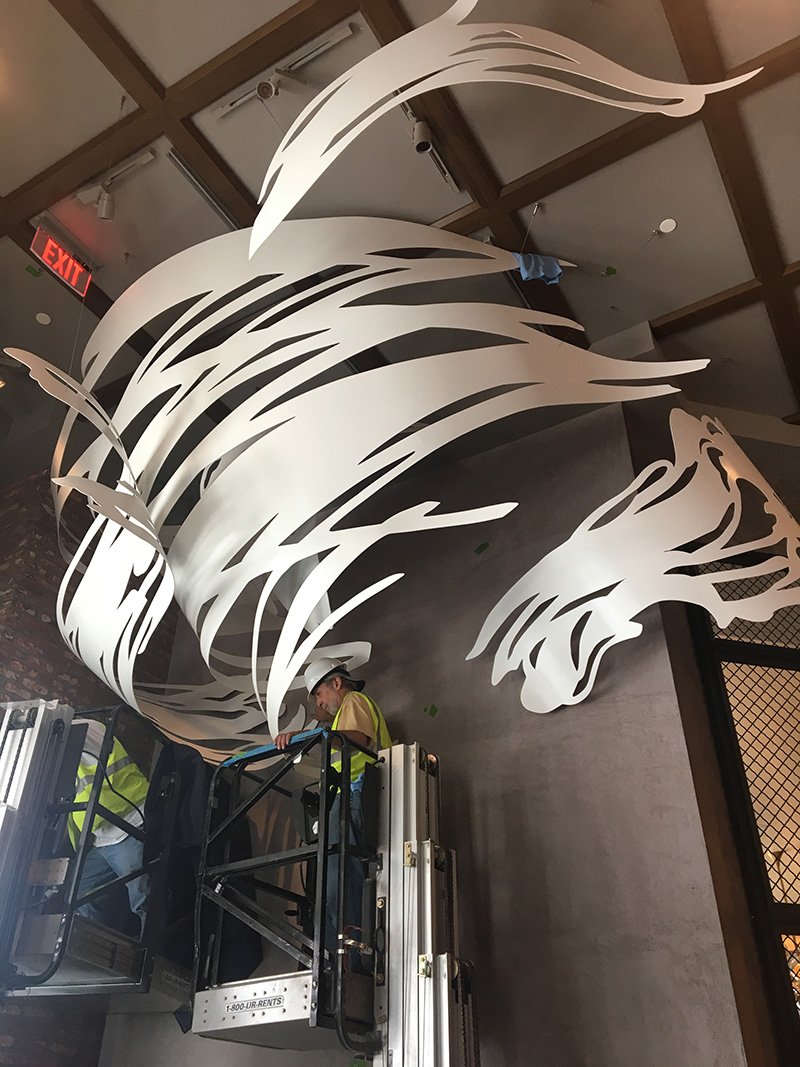
Taking shape!
These exhausted men are my heroes.
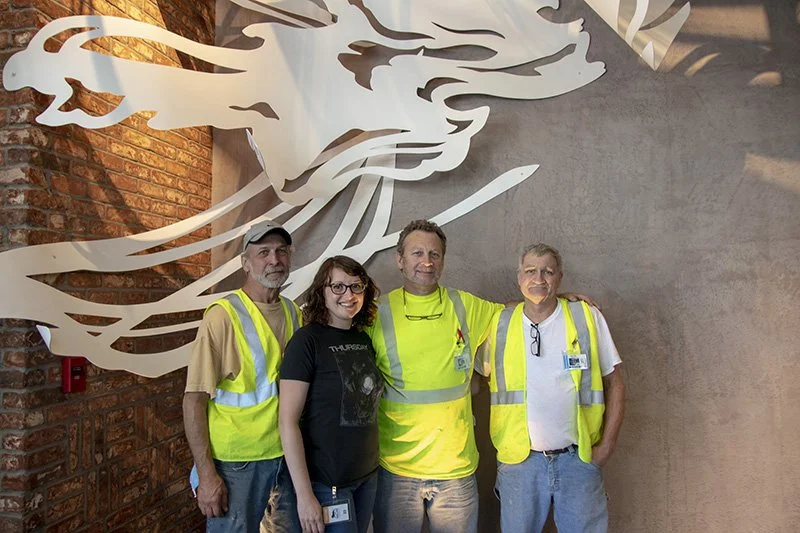
Finished! We survived, just barely, and lived to tell the tale. MGM is thrilled, and so am I. Huge thanks to everyone at RAREculture (art advisor), MGM (client), Polich Tallix (fabricator), Kris Collins of MGAC (project manager), and all of the kind people who helped make THE FLYING TIDINGS WHIRLED a reality.